Powering your shop-floor into the FUTURE!
In order to remain competitive in today’s complex manufacturing industry it is essential for companies to integrate ERP accounting with the shop floor. This is necessary for the effective management of the supply chain and the improvement of business processes. It also enforces conformance to standards and regulations and will ultimately lower costs.
It is for these reasons that Job Shop owners are implementing Enterprise Resource Planning (ERP) systems within their organizations with the aim of achieving a competitive advantage. Modern ERP systems now offer manufacturing capabilities. However, in the very specific and unique world of make-to-order, engineer-to-order and custom manufacturing industries, ERP systems are unable to handle the complex product batch runs that change constantly. This inherent inability of ERP systems to handle the real-world scenarios that custom manufacturing industries face every day has led to a divide between the Job Shop and the ERP systems. Integrate ERP accounting with the Shop Floor is critical to address this.
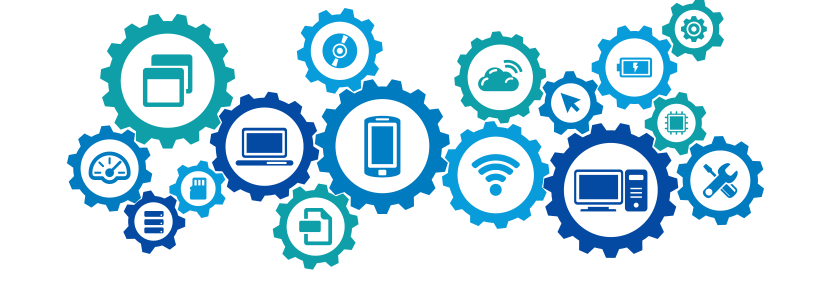
Fitting a Round Peg in a Square Hole
Many manufacturing organisations have attempted to integrate the Job-Shop and the ERP system with varying results. In some cases, organizations attempted to develop extensions to their ERP system to make the latter system more suitable for make-to-order / engineer-to-order environments. As a result this often led to a more sluggish accounting system. Another impact was a time-gap between Job-Shop activities and the information being posted to the ERP system. This in turn meant that the information management received was often outdated and prevented accurate decision making.
In an effort to overcome the above challenges, manufacturers should aim to integrate their ERP with a modern and powerful Job-Shop System that integrates in real-time. Management should be immediately notified of job shop changes; business intelligence tools should be used to increase visibility of the job shop. Information about the status of a customer orders, inventory shortages or excesses and quality control deviations should be at management’s finger-tips.
Reasons to Integrate ERP Accounting With Your Shop Floor
Seamlessly connecting job shop processes with the ERP accounting system therefore requires a tightly integrated yet flexible solution that leverages the latest technologies. In a make-to-order or custom manufacturing environment it is also imperative to be able to handle the changes customers throw at you quickly and efficiently. To solve these challenges, any Job-Shop System should at minimum meet the following requirements:
- Permit fast compilation of estimates & quotes that are reliably consistent;
- Offer full traceability and workflow visibility from inquiry through to dispatch;
- Full real-time ERP integration must offer Inventory & Procurement Management for inventory replenishment and buy-outs respectively;
- Failures detected by Quality Control (QC) auto-alerts management;
- Automatic time capture of the shop-floor activities permits comparisons to the original job estimates;
- Enable an holistic solution that provides a seamless integration between the Job-Shop System and the ERP.
It is clear from the above requirements that an organisation must implement a solution that offers end-to-end and real-time integration and Integrate ERP accounting with your shop-floor.
Download our 4IR E-Book now or contact us.
To partner with a company experienced in offering solutions specific to make-to-order and custom manufacturing environments, and integrating your ERP with the Shop Floor, contact us today!