How can software improve your shop-floor processes?
Index
- Introduction
- What is a Manufacturing Shop?
- What are the characteristics of a Manufacturing Job Shop?
- A Job Shop Manufacture Example
- Challenges of Job Shop Manufacturing
- How do Scaling-up shops Use Job Shop Manufacturing?
- Job Manufacturing and the JobPRO solution
- Closing the loop – Activity measurements
Introduction
UniSource designed and developed JobPRO – Job Shop & Service Management Software for the manufacturing job shops as a result of the frustration of our manufacturer clients, who could not to find a suitable tool for production management. All the solutions available on the market were either too complex, ridiculously unaffordable, or exhibited a clumsy interface – with JobPRO we knew we could lead the way with a solution specifically dedicated and designed for manufacturing Job Shops in the SME space.
We had also – in the 13 years prior, leading up to the inception of JobPRO – been providing ERP application consulting and support on numerous ERP manufacturing software packages, but none addressed (was designed for) the make-to-order / repair-to-order / make-to-stock) needs of our manufacturing clients . Pivoting on the previous 13 years of experience with our clients we employed the foundation principles in the design of the software that every modern job shop manufacturer should follow.
This e-book is aimed at manufacturing job shops who want to broaden their know-how and find techniques and methods to improve the way they run their business regardless of whether they are mature manufacturers with a proven success record or new Start-ups.
Do spend a few minutes – we promise you will not be bored – reading these Industry expert insights!
- What is a Manufacturing Job Shop?
- Challenges of Job Shop Manufacturing
- How Manufacturers that scale-up use Job Shop Manufacturing
- JobPRO job shop manufacturing software in practice
- The feedback loop – Shop-floor Activity Tracking & measurement
What is a Manufacturing Job Shop?
Today, like most days, James – the Production Manager of a Make-to-Order MTO PRODUCTION Job Shop – is driving to work his mind already preoccupied (not taking notice of the crawling bumper-to-bumper traffic) – with the customer demands his job shop is as per norm having to deal with. He is having to re-schedule the work re-runs that resulted from the previous day’s failed Quality Inspections and still having to ensure he meet his clients deadlines, notwithstanding his performance incentive targets that are looking miserable and falling short owing the latter chaotic demand.
For months he has been thinking ‘there must be a better way’
So, what can be done, ‘can I throw technology at these challenges?’
Let us get a more in-depth look at the challenges James is facing daily in the world of the job shop manufacturing process.
What are the characteristics of a Manufacturing Job Shop?
This manufacturing business characterizes itself as a shop which has tools, machines, and facilities which have a similar kind of function or performance. The separated workstations (Work Centre machines) perform different tasks (Activities) during a products manufacturing process.
The final products come produced in small batches (of varying quantities). Customers customize their orders to meet their specific needs.
This means a business will produce a small volume of products which are not standardized.
The level of personalization offered by this process means the shop floor has a unique set-up and process steps. Products produced by a company may not flow in the same direction. Meaning items will follow a different workflow with the next process and may even return to the same machine (a Lathe, a CNC, a Drill, etc.) several times. All this depends on the products manufacturing requirements.
Typically, Job shop manufacturers, produce parts (Repair-to-Order, Engineer-to-order repair or engineer parts) for other businesses and use a Just in Time (JIT) workflow to fulfill customer orders .
Business owners who use this type of process usually use a Just in Time workflow (JIT) workflow to fulfill customer orders.
A Job Shop Manufacturing Example
Whilst there are hundreds of different Job Shops let’s look at an example of industrial pumps Manufacturer receiving a repair-to-order request from a customer. He will need to assess, quote and repair the pump before dispatching back to the customer.
- Receiving of customer’s assets (pumps)
A pump (hereafter referred to as a Part) is delivered to the workshop and is ‘received’ into the Black-book and given the next receipt-no. The pump now sits in a Queue await assignment of labour.
- Stripping
In order for an engineer to make a technical assessment (diagnosis) the Part needs to be stripped down – one or two ‘Strippers’ are assigned the ‘Activity’
- Technical Assessment / Activity selection
- Estimate Preparation & Quoting
- Quotation approval (Internal)
- Await Customer Purchase Order
- Kick-start Production
- Materials Requirement, Procurement and Stock Issues
- Inventory Issues
Workshop / Shop-floor Activities These Activities often have follow complicated Workflows that present challenges to the production foremen. Visibility of the Part’s progress from work-Centre to Work-Centre through each Activity is crucial for effective planning and customer feedback.
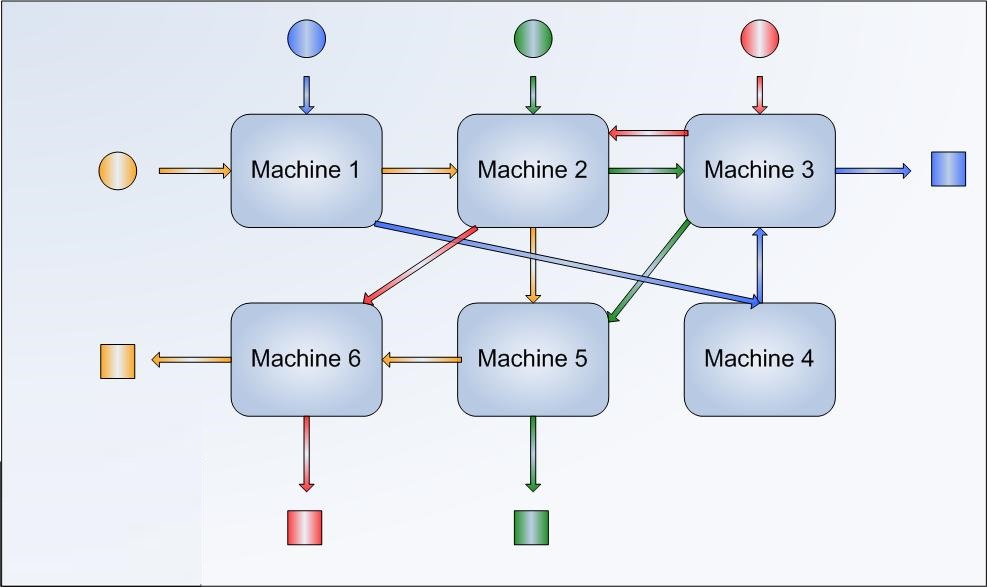
- Dispatch & Invoice
If you pause for a moment and reflect on the job production process it is evident that those managers that run Job Shop Manufacturing business are a special breed and – it is not for the faint-hearted, given the obstacles confronting them.
PROFESSIONAL TIP: But before we dive further into this world – Are you a scaling business manufacturer wanting to scale up and wanting to achieve a step-function int your overall? Check out this must-have guide to answering the question of Industry 4.0 (4IR) in Manufacturing
So, let’s explore further:
Challenges of Job Shop Manufacturing
1. Customer demand imposes complexity
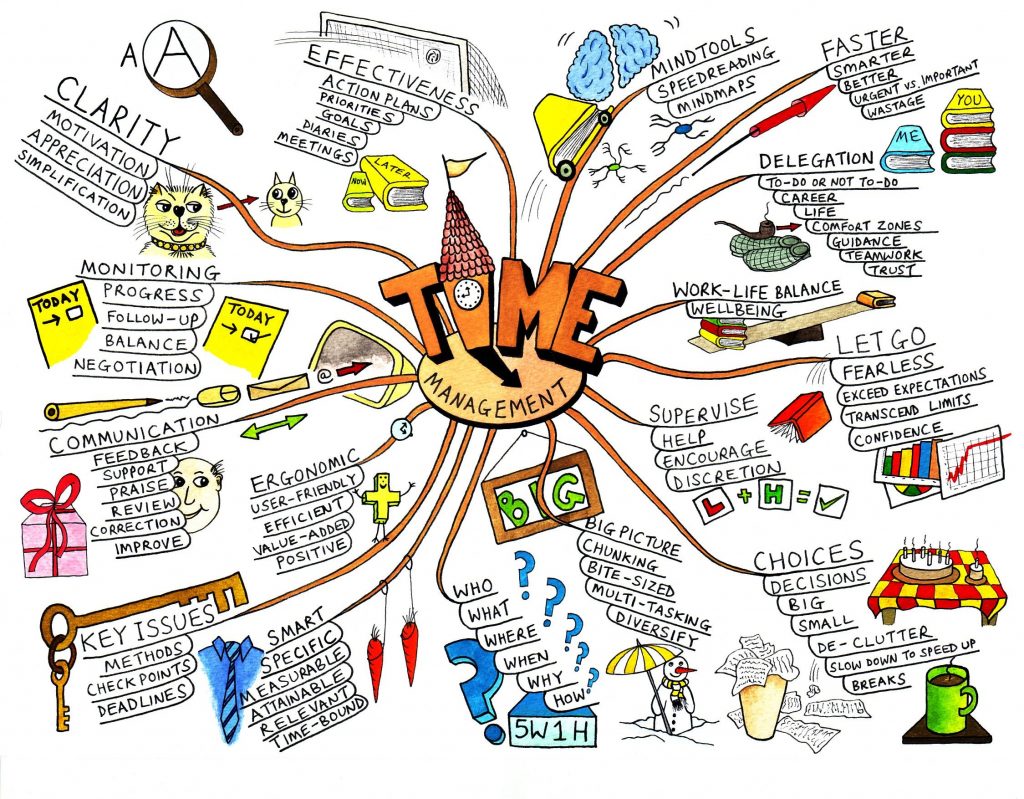
The randomness and variability of customer demands can often lead to a backlog of orders – ‘the nature of the beast’ for job shop manufacturers. The variations in order quantities and frequency, playing havoc with workflow schedules that may need to be constantly changed to meet this variation in customer demand.
Discover how to how technology can enforce your business process-flow rule cementing consistency
2. Difficult to control Production Flow
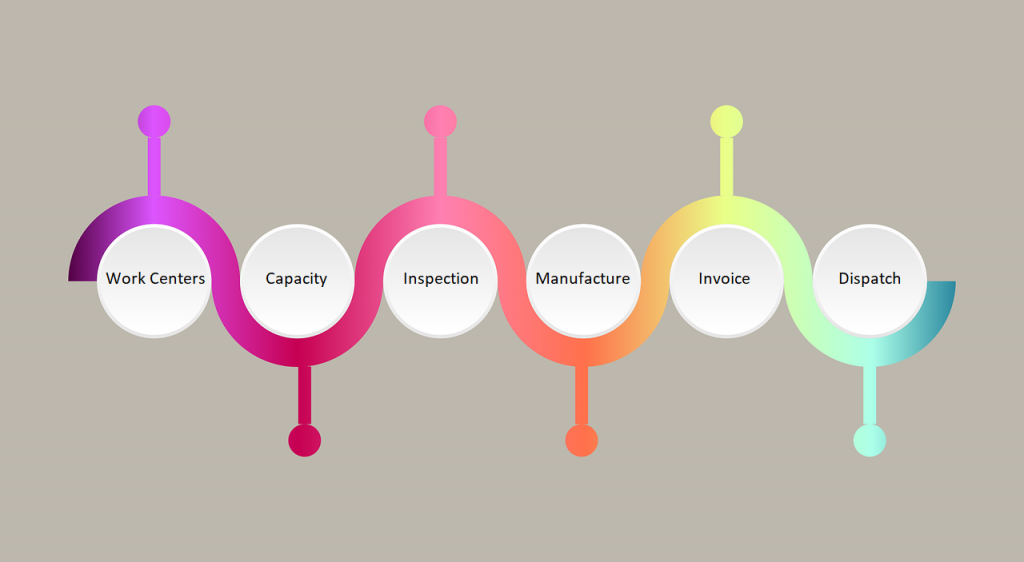
Because Parts follow different processes, it can be a ‘head-ache’ to organize your production flow. Some jobs can be relatively straight forward, whilst others can run into difficulties that mandate work re-runs.
Discover how to how rendering visibly offers control and tracking of shop-floor Activities
3. Difficult to ensure consistent pricing
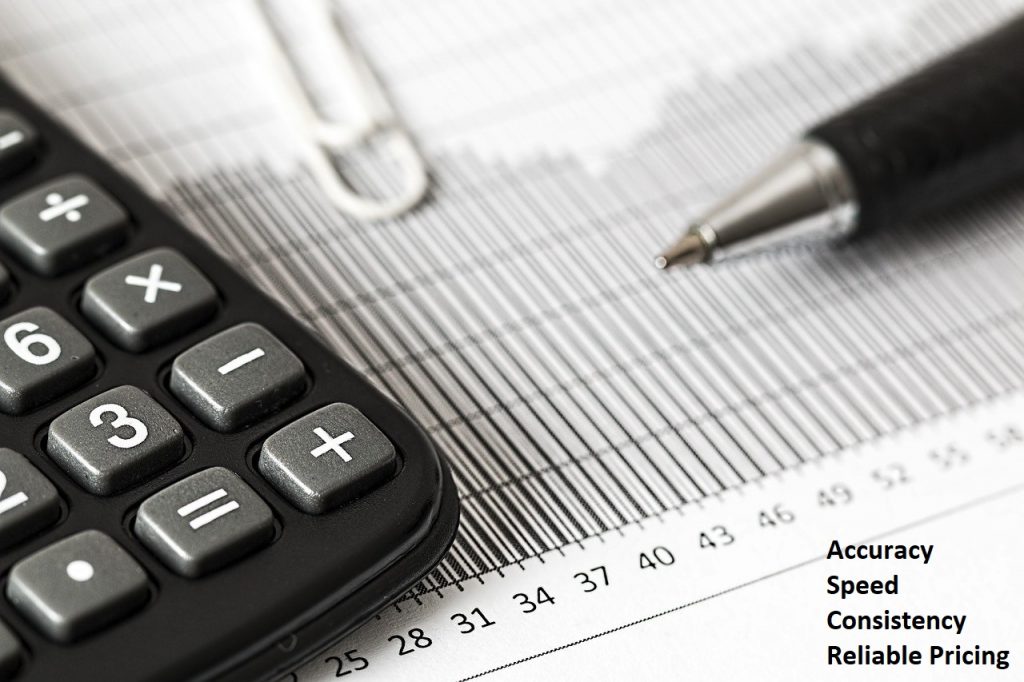
Working from Excel impedes your ability to enforce consistent pricing that ensures your margins. Tools, like Excel, do not have direct electronic access to your price lists stored in the accounting / ERP system. Importing pricelists and keeping them up to date in an excel spreadsheet creates manual work that is fraught with potential for the proverbial ‘finger-problems’
Discover how to ensure 100% error-free consistent pricing
4. High Production Lead Time
Even Contract Manufacturers need to await a customer purchase order (PO) because items are customizable. In hustle and bustle of everyday demands you may not be aware that PO has arrived – and failing to kick-off procurement and production as soon as you have received the PO will lead to compromising your Order-to-delivery KPI.
Discover How technology can assist – Alerts reduces Order-to-delivery cycles
The disadvantages of a job shop perhaps appear daunting. While the risks are real, there are ways in which you can manage or avoid them.
How do Scaling-up shops Use Job Shop Manufacturing?
As already mentioned, one of the biggest issues a production manager and / or business owner finds is juggling the varying customer demands placed on their workflows and materials procurement. Some managers resolve these hurdles is by tracking their key performance indicators.
Managing the following KPI’s has resulted in significant improvements which are key to scaling up the whole operation:
- Tighter inventory control
- Controlled workflow: from pre-shop floor to shop-floor process flow
- Visibility of the full process – recording the Order-to-Delivery cycle time
- Reducing work-Re-runs
- Tracking Pricing inconsistencies
Finding a way to ‘get it right first time’ is an ongoing activity of establishing incremental improvements to achieve a ‘repeatable’ controlled-process, time and time again, job after job.
Repeatable & Controlled Process
One of the major disadvantages of running a job shop is ensuring that your production process from order-to-delivery and from Invoice-to-cash is a repeatable process whereby your business rules, workflows and pricing are applied consistently to improve productivity.
Supply Chain Management – Procurement driven by the Job
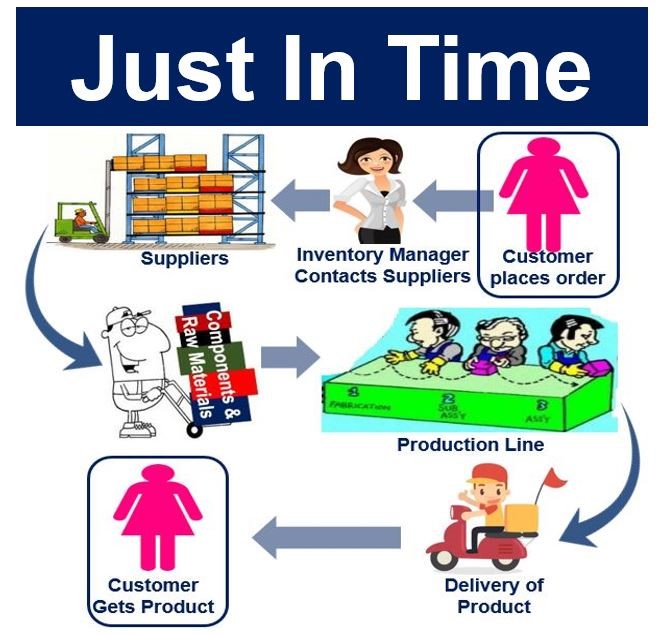
Ensuring you have identified the required materials and these are delivered expediently by your suppliers and only in the required quantities for the job, is an essential to preempt delays and cost over-runs.
Mastering of the supply chain is critical whether you are a Start-up or a manufacturer scaling up. Most make-to-order job shops hold minimal levels and only essential fast-moving materials (consumables) mandating J.I.T KPI – how Procurement driven by the Job applies JIT.
Integrated Accounting (ERP)
Manufacturing Lead time in job shops is contingent with the arrival of the customer’s order – only after confirmation of your customer’s order can production commence (assuming all materials available). Manufacturing lead time from PO-to-ReadyForDelivery impacts on your service levels – YOU do not want to keep them waiting.
This means a lot of manufacturers want to scale up and move from the spreadsheet-tool to an integrated job production & inventory management solution software.
See Time to Dump the Spreadsheet
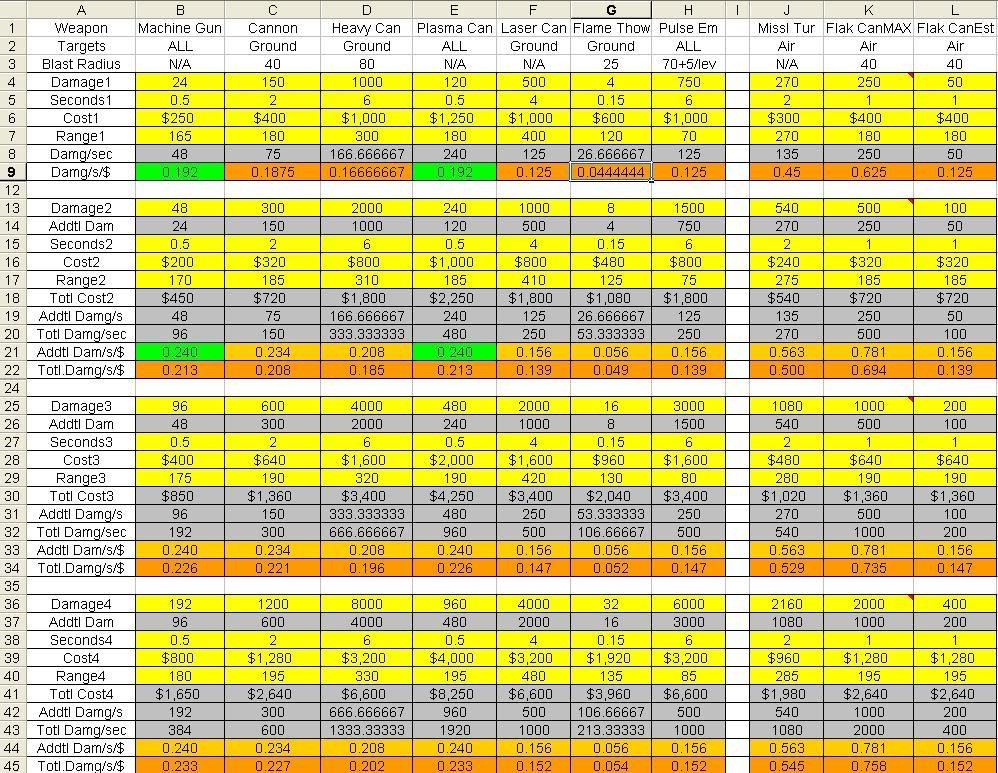
But what if there was a product that did so much more than assist with inventory management?
Effective ERP integration goes far beyond just integrated inventory management, it is also about having a seamless and holistic solution. A fully integrated ERP solution allows for the shop floor team and foremen to operate on a platform that resonates with their world. We accept that integrating ERP will provide accounting for accountants, purchasing management for buyers, sales information for the sales-reps, but what about the artisans on the shop-floor?
What about the technicians / engineers performing technical assessment of the Part requiring repair (or manufacture)? Why not perform these functions and interact directly with the Job Production shop-floor module on the shop-floor?
What if there was a Solution that offered much more than a collection of modules serving certain specialised functions in the organisation but instead integrated all your job production departments together as one business. A Solution that overcomes the challenges of managing a fragmented and disjointed set of departments – giving you full comprehensive visibility of the business workflow, from Order-to-delivery and Invoice-to-cash?
Job Shop Manufacturing and the JobPRO solution
“Most managers react to the confusion in their job shops in one of two ways. Either they turn to outside vendors for the latest in automation technologies and production control software—an expensive response that seldom delivers the promised benefits—or they throw up their hands.” – Article from Harvard Business Review, 1989.
Whilst this quoted passage was written a 3 decades ago, it still holds truth. Most MRP / ERP systems are developed in mind for large corporations with employee counts in the 500+ range and come with premium price.
As mentioned in the introduction, JobPRO – Job Shop Manufacturing software was designed specifically to suit and fit the unique requirements of integrating existing ERP or accounting systems to the shop floor for the make-to-order, engineer-to-order, repair-to-order and make-to-stock job shops.
JobPRO offers your job shop the tools to monitor and view of all your business processes with one holistic view. That brings to you the improved control and ensures the consistency you desire.
Our JobPRO Software offers you:
Job Shop Manufacturing and JobPRO
Closing the loop – Activity measurements
Workcentre Tracking & Routing
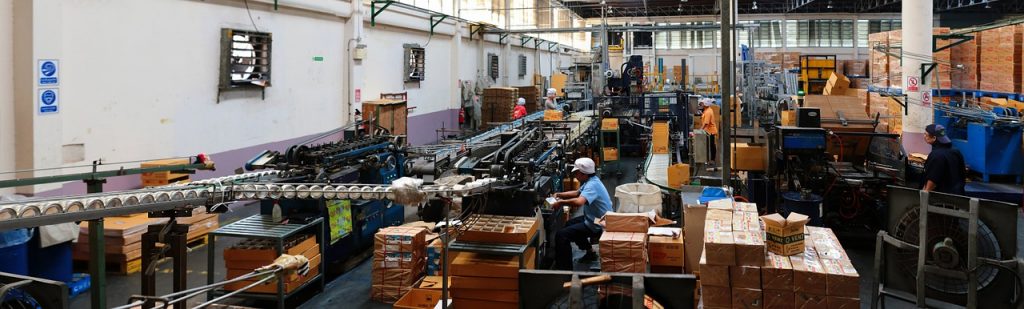
Tracking – On the shop floor , as the production manager or foreman you need a tool to view the Queue of jobs lined up and receive constant feedback on the Work Centre activities – “is the ‘Turning’ Activity completed?” or “What is the next Activity on this job’s workflow”?
Routing – A Workcentre Tracking & Routing tool makes it easier to keep your shop floor routing workflow dynamic too. Your routing needs to fully utilize your resources efficiently ( the machines and the highly skilled artisans)
Estimation Verification – The Workcentre Tracking & Routing tool also offers another critical component that will allow your business to scale-up – the ability to measure the Actual-Time each Activity takes. This can be reported on a dashboard presenting visually comparisons between Actuals vs estimates, which WorkCentre’s are more efficient and / or what Activity-estimates need to be revised.
Download our E-book now or sign up for a free consultation.
To partner with a company experienced in offering solutions specific to make-to-order and custom manufacturing environments, contact us today!