Take Control of Chaotic Shop-Floor Scheduling processes
Many job shops struggle to meet and maintain deadlines, this is owing to manually driven jobs. Either by excel or manually printed job cards or documents. With a manual process service work flows are generally not maintained and time spent on a job is not accurately recorded. Can you improve your business operations with a Job Scheduling?
Many make-to-order, small fabrication engineering businesses, struggle to meet promised deadlines and even quality control can suffer, due to manual systems and a lack of proper overall supervision.
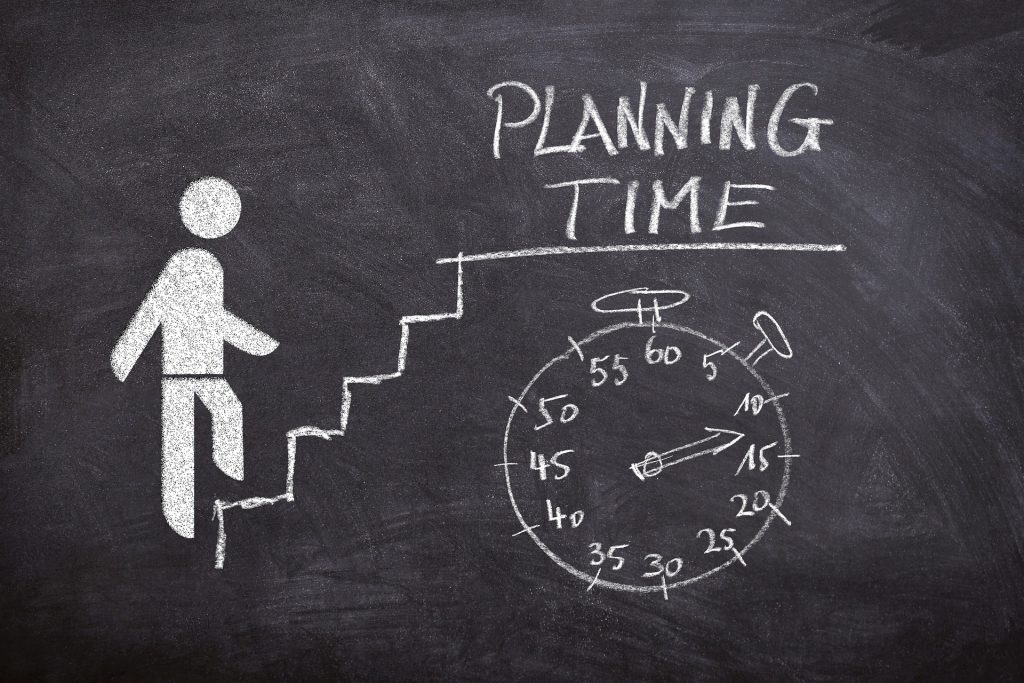
Why tracking time spent correctly is important?
With a manual job card system, Owners and foreman’s find it hard to get artisans or shop-floor employees to fill their job cards correctly. Many problems experienced are owing to the fact that artisans do not fill in the job cards timeously. Sometimes job cards are only completed in a weeks time or at the end of the shift, this inherently comes with its own problems as staff don’t remember the time they spent on a certain job which then creates a situation where time is not accurately costed on. Many Manufacturing work-shops find that they are under quoting and losing money.
Under quoting is not good for business and your cash-flow, subsequently over charging can also hurt your business. You may start losing business to your competitors due to the fact they are generally cheaper than you. So it is imperative that estimates are done correctly and should be very low variance in pricing. One way of achieving better costings to your customers is moving onto an automated system that assists you with complex quotes and able to schedule the correct time on the different work centre’s.
A lot of business owners also struggle with capacity planning, with many job cards and no overview of the operation, it is hard to understand how much work you have and this strategy can work against you. When you promise delivery dates and you do not meet them, this can negatively impact future business for your manufacturing operations.
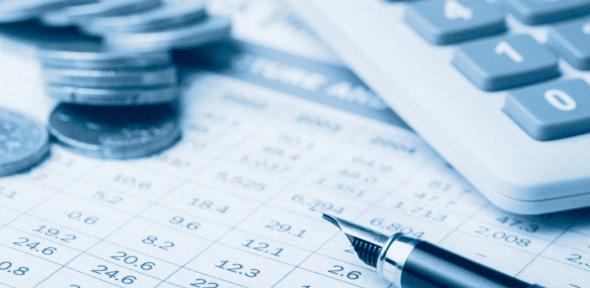
Better costings with a Job Scheduling
With an automated software solution you can better cost your quotes from actual costs pertaining to different rates on artisans, but you will also account for the different rates used on machines such as a lathe.
Many business owner struggle or do not know the actual cost per hour on a job because artisan and machine rates are not calculated correctly and sometimes is a thumb suck for costings which could land you under or over quoting on a job. Many Job Shop manufacturing owners require consistent activity based costing.
Under promise and over deliver!
With proper tools, you will be able to estimate better on quotes and delivery times. With an automated system you will have full visibility of all jobs from enquiry to dispatch. You will be able to give snap feedback to your customers on the status of their jobs.
Is there a solution for you?
With JobPRO and JobTrak we can assist you with visible job tracking, consistent quoting, better costing and capacity planning Job Scheduling solution. With our solution you can set service workflows from pre shop-floor processes to shop-floor processes, so a user can drive the job from receiving the enquiry to routing the job through the different work centre’s( from lathing to drilling to machining)
Download our E-book now or sign up for a free consultation.